Blog: Decarbonising the global steel and cement sectors requires more than zero carbon fuels: analysis
Attachments
Introduction
As part of our ongoing investigations into the decarbonisation of various sectors, our latest study looks at the emissions from the steel and cement industries (previous publications focused on transport, buildings, power). It’s a difficult nut to crack, as large chunks of the emissions are not related to conventional fossil fuel combustion.
With decarbonisation, we normally think of energy-related measures such as higher energy efficiency, electrification of demand, zero-carbon fuels and a zero-carbon electricity supply in order to move towards net-zero CO2 emissions. While such measures could set, say, the buildings and transport sectors onto an emissions pathway compatible with the Paris Agreement’s 1.5°C long term warming limit, this is not so easy for industry, especially in steel and cement production.
We looked at three different scenarios for both these industries, using country case studies for each. One follows current trends, one represents a shift towards decarbonisation of the energy supply, and one represents steps towards circular value chains. We also highlight the extent by which other step-change technologies can “close the gap” to net-zero emissions.
What we found was that decarbonisation of both the steel and cement industries with technologies currently available—even when including some kind of shift towards a circular economy (which involves moving away from linear to circular value chains, generally meaning a shift from “Take, Make, Waste” to “Reduce, Reuse, Replace, Recycle”)—would not be enough to achieve the deep cuts in GHG emissions needed to be in line with the Paris Agreement. The combined effect is estimated to be an around 30%–50% reduction compared to current trends by 2050, which is a good start. However, further measures are needed to reach net zero emissions across the economy, including the industry sector, in the second half of this century.
If we are to reach the Paris Agreement’s so-called “net zero” emissions by the second half of this century, we are going to need solutions to both of these industries. We need an increase in research and development (R&D) into innovative new processes, as well as materials substitution.
Steel
In 2015, around five percent of greenhouse gas emissions came from the steel industry – accounting for around 2.8 gigatonnes of CO2. Worldwide, roughly 70 percent of steel is produced through the blast furnace/basic oxygen furnace system (BF-BOF), which converts raw materials such as coal, iron ore and limestone, to pig iron in the blast furnace, and subsequently into steel in the basic oxygen furnace.
The other third is produced through an electric arc furnace (EAF), which primarily uses electricity to make steel, mainly from scrap steel feedstock. A shift towards EAF would thus help the steel sector move towards a circular value chain. The energy intensity of this process is around one third of the BF-BOF process.
Due to its electricity-intensive nature, the EAF route combined with renewable power could contribute to the decarbonisation of steel making. In contrast, the decarbonisation potential of the BF-BOF route is more limited due to the integral role of coal in this process, which can only be partially replaced by lower carbon fuel sources.
We modelled three different scenarios to look at how the steel industry could reduce emissions in the future based on existing technologies. We focused on China and the EU - two steel producers in different stages. In the EU, steel production peaked in 2007, dropping by 21 percent to 2015, but is expected to grow by a small amount to 2050. In China, steel demand doubled from 2005-2015, and is expected to peak in the next decade. These projections do not take into account reductions in steel demand from material efficiency measures.
China will most likely achieve large emission reductions due to decreasing demand for steel. Energy efficiency improvements will also contribute. By contrast, emissions in the EU will only modestly decrease even under our most ambitious scenarios, as production is not projected to change strongly from today’s levels, and scrap recycling is already at comparatively high levels today. Overall, none of our scenarios can reach net zero emissions by 2050. One of the main barriers to decarbonisation identified by this analysis is the limited availability of scrap steel which prevents a larger share of EAF steel production.
Decarbonising steelmaking therefore requires looking beyond these scenarios based on currently available technology. To rapidly decarbonise the steel sector, investments must be made to intensify R&D, demonstrate and introduce to the market innovative steel production routes such as processes that integrate carbon capture and storage (CCS), electrolysis using renewable energy or a route using renewables-based hydrogen.
Transitioning to circular economy strategies can further reduce steel demand. This could include implementing measures to increase material efficiency, such as lightweight product design, increasing product lifespans, using products more intensively, and better manufacturing processes. In addition, transitioning to circular product designs that enable the re-use of steel without melting and the substitution of steel with lower emissions-intensive materials, such as aluminium and plastics in vehicles, can also lower steel demand.
Cement
Cement-related emissions have nearly doubled their share of global greenhouse gas emissions, rising from nearly 1.0 Gt in 1990 to over 2.6 GtCO2e in 2010, from 2.8 percent to 5.5 percent of global GHG emissions. This increase was largely driven by the growth of cement production in China (which increased more than tenfold since 1990).
Worldwide, cement production is projected to keep rising, mainly driven by growth rates in the developing world—chiefly in South Asia and Sub-Saharan Africa, where cement industry has boomed in recent years.
For cement, we looked at three very different regions: the EU, China and Nigeria.
European cement production has been mostly stable, decreasing recently in the wake of the 2008 financial crisis. China’s production has risen continuously since the turn of the millennium, but is projected by some to peak very soon and according to others may have already done so. Nigeria’s cement production took about a decade longer to reach comparable growth rates; it is now the largest cement producer in Sub-Saharan Africa, and exceeds the growth rates of China observed in the last two decades.
Cement making consists of two distinct steps: clinker production, followed by blending of clinker into cement in a cement mill. Emissions from the cement industry can be grouped into three categories: process emissions, direct energy-related emissions and electricity-related emissions.
The process emissions occur when limestone is converted into clinker, and CO2 is released as a by-product, making up around 50 percent of cement-related emissions. Therefore, substantial emissions remain in even the most ambitious of our scenarios, as decarbonisation in the form of efficiency, electrification, and a shift to zero-carbon electricity supply cannot address these.
The presence of process emissions means that even under decarbonisation and a limited move towards circular economy measures (partial substitution of clinker in the cement production process, and partial substitution of cement needed to make concrete), substantial emissions will remain. To help mitigate these emissions, innovative options for low-carbon products as replacements for cement or for concrete, such as Cross-Laminated Timber, and possibly the large-scale use of CCS, will be necessary.
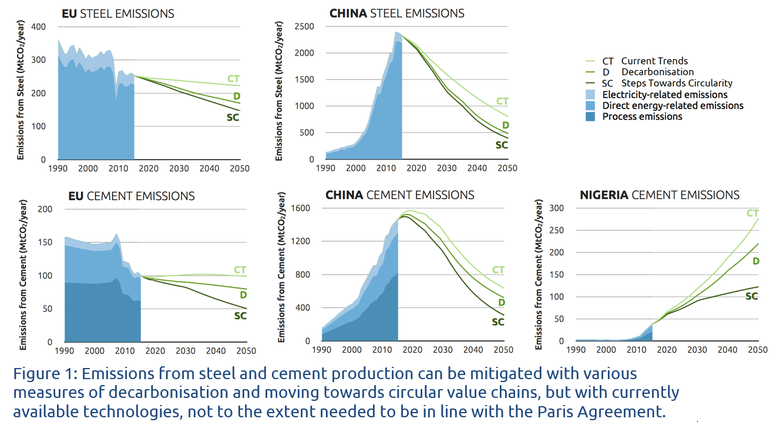
Conclusion
In summary, the options conventionally implied by decarbonisation—efficiency increases, electrification, and shift to zero-carbon power supply—will not be enough to set heavy industry on a Paris-compatible pathway. Substantial chunks of emissions would remain unaddressed by such measures.
In the steel sector, the limited availability of scrap for electric steel recycling constrains the possible shift away from blast furnace steelmaking. In the cement sector, the chemical reaction involved in clinker production results in emissions that cannot be reduced unless the need for clinker itself is reduced.
A significant and immediate increase of research and development into innovative low- or zero-carbon production routes, materials substitution (e.g. aluminium, wood), and the use of CCS, are needed if steel and cement—global demand for which is projected to continue rising in the coming decades—are to be Paris-compatible.
Decarbonisation memo series

This memo is a part of the CAT decarbonisation memo series that seeks to address the question: How can different sectors achieve the rapid transformations and emissions reductions required to meet the long-term temperature goals of the Paris Agreement? Click on the link below to read more about the series or click on the icons to see the analysis for each sector.
Stay informed
Subscribe to our newsletter