Decarbonising the iron and steel sector: China, India and the US
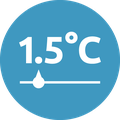
By Norah Zhang, Anna Nilsson and Cindy Baxter
Iron and steel production currently contribute around 7-8% of global greenhouse gas (GHG) emissions, so decarbonising this sector is fundamental to reaching net zero and meeting the Paris Agreement's 1.5°C warming limit.
Traditionally seen as a "hard-to-abate" industry, the steel sector now has viable pathways to decarbonisation, driven by recent technological advancements, policy commitments, and private investments. However, while decarbonising the steel sector is technically feasible, countries face different challenges in making this happen at the pace needed.
We've just published this analysis that looks at the specific challenges faced by three countries: China, India and the US - to highlight what's needed to make progress in decarbonising their steel sectors. By understanding these factors, this report lays the groundwork for our future work in developing tailored national benchmarks.
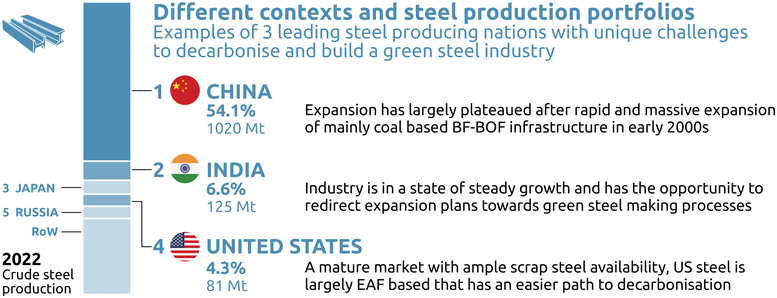
The major steelmaking approaches and their corresponding emission reduction pathways
Key challenges
The main challenge for the steel sector is shifting infrastructure from today's predominant blast furnaces that run on GHG-intensive coal-derived coke to electric arc furnaces (EAFs) running on clean power that process scrap steel, or direct reduced iron (DRI) produced with zero carbon feedstocks, such as green hydrogen.
The specific challenges each country faces differ substantially according to the status of the steel industry and its likely future development. Determining the fastest possible speed of action therefore needs to take these challenges into account.
We look at each of the three countries to show how current circumstances and projected demand for steel determine what a path to a net zero steel production could look like. Three big differences between the three countries are:
- The stock and age of existing infrastructure for various technologies
- Future trends in steel production and capacity
- Factors that limit the potential for lower GHG-intensive steel production, such as scrap steel availability and access to high-grade iron ore
Over the coming decades each country will face unique challenges and will have to identify their priorities for decarbonising their steel sector:
- China, as the world's largest steel producer, should find routes to decommission its Blast Furnace to Basic Oxygen Furnace (BF-BOF) capacity, replacing it with green steel production where needed, and expand scrap recycling through new electric arc furnaces (EAFs).
- India needs to focus on integrating clean technologies, such as green hydrogen, into its rapidly growing steel industry while ceasing further investment in and construction of BF-BOF plants.
- The US has a well-established steel industry that relies heavily on scrap steel recycling: it should prioritise decarbonising power generation as well as further electrifying the steel sector.
Access to CCUS technology
Despite the scaling up of CCUS globally, its application in the steel industry remains limited, with no commercially operating CCUS facilities on the highest-emitting BF-BOF plants. Currently, only one steel plant in the world operates CCUS at a commercial scale—the Al Reyadah CCUS-EAF plant in the UAE—which captures just 19-26% of CO2, primarily for enhanced oil recovery.
CCUS technology does not efficiently and cost-effectively reduce emissions from BF-BOF steelmaking, whether retrofitting an operating plant or rebuilding a new one. Lastly, CCUS cannot be an excuse for continuing the construction of new coal-based capacity.
Priorities for decarbonising the steel industry
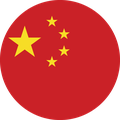
China
As the largest steel maker and the home of the most blast furnaces in the world, China's action greatly determines the pace of decarbonisation in the global steel industry. China’s steel production has roughly stabilised and is expected to decline from 2025. The reduced production will be mainly driven by the reduced demand for steel in the building sector. However, reducing production alone is not enough to achieve a 1.5 compatible steel industry, and the decarbonisation of the steel production chain is more critical.
The retirement of the emissions-intensive blast furnaces will be at the centre, with a halt to new coal-based steelmaking plants as an important step. 80% of the currently operating BF-BOF capacity in China was commissioned in the last 40 years and is still within the average life expectancy. Early retirement of these steel plants poses a significant stranded asset risk but will be necessary to some extent in order to stay in line with the Paris agreement.
A holistic strategy is imperative to achieve a net zero steel sector in China by 2050 - the capacity gap resulting from the BF-BOF phase-down will be addressed by the construction of EAFs running on clean energy.
Increasing supplies of scrap steel and expanding green hydrogen production provide opportunities for this transition. Simultaneously, China must reduce its dependence on coal for power generation and explore alternative sources for high-grade iron ore.
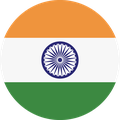
India
Given India's rapid economic development, urbanisation, and infrastructure construction, the steel industry is poised to assume a significantly more vital role in the country.
However, the exponential growth in capacity and production raises concerns about a potential quadrupling of carbon emissions from India's steel sector by 2050 if coal still dominates. Meanwhile, this growth presents India with a unique opportunity to foster a low-carbon steel sector by minimising new BF-BOF and coal-based DRI builds and transitioning to electrified steelmaking.
Prioritising the adoption of cleaner EAF technology for future steel production capacity growth is imperative, alongside decarbonising the power sector. To achieve significant decarbonisation and reduce reliance on the coal-based BF-BOF route, halting new project constructions is essential.
India has an advantage in terms of abundant domestic high-grade iron ore reserves and has the potential to prioritise DRI-EAF steelmaking, which can be decarbonised by using green hydrogen. Scarcity of scrap limits the expansion of secondary steelmaking. Through government efforts to incentivise scrap recycling and formalise the scrap market, scrap-EAF has the potential to satisfy around 20% of India’s future steel demand.
Currently, available technologies for steel decarbonisation are still in a nascent stage in India. Global climate finance, private sector investments, and technology support are therefore crucial to accelerate India’s transition towards a Paris-aligned steel sector.
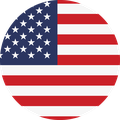
The US
The US, benefiting from ample scrap availability, holds a leading position in steel decarbonisation endeavours, positioning it to lead the global transition towards a fully decarbonised steel sector.
Further decarbonising steel production in the United States requires ambitious actions and concrete measures. While initiatives like the Inflation Reduction Act and Bipartisan Infrastructure Law are boosting the US steel market, they also create openings for emerging technologies such as green hydrogen, which can significantly reduce emissions.
Priority should be given to deepening electrification and achieving the goal of a carbon-free electricity system by 2035, considering the substantial share of EAF capacities in the US. As scrap-EAF remains central to steelmaking, EAFs are also used for primary steelmaking with DRI. Transitioning from natural gas to green hydrogen for DRI production offers considerable potential for decarbonisation.
Stay informed
Subscribe to our newsletter